بررسی اجمالی
سیستم های تبرید در صنعت فرآوری گاز طبیعی و فرآیندهای مرتبط با پالایش نفت، پتروشیمی و صنایع شیمیایی رایج هستند. چندین کاربرد برای تبرید عبارتند از بازیافت NGL، بازیابی LPG، کنترل نقطه شبنم هیدروکربن، تراکم رفلکس برای خردکننده های هیدروکربن سبک و کارخانه های LNG. انتخاب یک مبرد به طور کلی بر اساس نیازهای دما، در دسترس بودن، اقتصادی بودن و تجربه قبلی است. به عنوان مثال، در یک کارخانه فرآوری گاز طبیعی، اتان و پروپان ممکن است در دسترس باشد. در حالی که در یک گیاه الفین، اتیلن و پروپیلن به راحتی در دسترس هستند. پروپان یا پروپیلن ممکن است در کارخانه آمونیاک به دلیل خطر آلودگی مناسب نباشد، در حالی که آمونیاک ممکن است به خوبی به این هدف عمل کند. هالوکربن ها به دلیل ویژگی های غیرقابل اشتعال آنها به طور گسترده مورد استفاده قرار گرفته اند.
فواید
شرکت مهندسی دلهام با مهندسی هر بسته تبرید با جدیدترین نرمافزار شبیهسازی فرآیند، سیستمهایی را مطابق با نیازهای خاص سایت طراحی و میسازد. طراحی دقیق تجهیزات عملکرد، عملکرد، قابلیت اطمینان و ایمنی را در نظر می گیرد.
طراحی بسته بندی فشرده
عملیات آسان
ظرفیت تبرید بالا
کاهش زمان و هزینه در محل
کاربردها و علل معمولی
شرح فرایند
شکل 1 یک شماتیک ساده از یک سیستم تبرید را نشان می دهد. کمپرسور مبرد تبخیر شده را فشرده می کند و سپس کندانسور بخار را به مایع تبدیل می کند. مایع از انباشته عبور می کند و سپس در یک شیر انبساط منبسط می شود که باعث می شود چشمک بزند و دمای آن به میزان قابل توجهی کاهش یابد. بخش مایع این فلاش مبرد است که سپس به یک مبدل حرارتی (چیلر) می رود. اساساً رایجترین نوع چیلر مورد استفاده در صنعت پردازش گاز، نوع کتری است. مبرد به داخل پوسته کتری منبسط می شود، جایی که سطحی برای غوطه وری کامل لوله فرآیند حفظ می شود. در چیلر، مبرد مایع گرما را از جریان فرآیند (گاز شیرین مرطوب) جذب میکند که دمای جریان فرآیند را به -12 درجه سانتیگراد کاهش میدهد. گرما مبرد مایع را تبخیر می کند. سپس سیستم این بخار و بخار را از اسکرابر مکش L.P به کمپرسور برمی گرداند تا چرخه تکرار شود. سیستم های فشرده سازی-انبساط بخار را می توان در اندازه های مختلف ساخت. این سیستم ها همچنین می توانند به دمای بسیار پایین برسند. این سیستم ها می توانند به دمای -15 درجه سانتیگراد دست یابند تا گاز شیرین را مایع کنند.
طراحی سیستم
اجزای ضروری هر سیستم تبرید به شرح زیر است:
اسکرابر مکش L.P: گازی که به کمپرسور نزدیک می شود مرطوب است. آثار مایع آبی یا آلی اغلب به صورت متناوب و بی صدا به کمپرسور آسیب می رساند. برای عملکرد جداسازی بهینه، درام های ضربه ای کمپرسور با در نظر گرفتن بسیاری از عوامل، با عناصر حذف کننده غبار مناسب در پیکربندی های صحیح طراحی و اندازه مناسبی دارند.
کمپرسور: در سیکل تبرید، کمپرسور دو وظیفه اصلی در سیکل تبرید دارد. یکی از عملکردها پمپاژ بخار مبرد از اواپراتور است تا دما و فشار مورد نظر در اواپراتور حفظ شود. عملکرد دوم افزایش فشار بخار مبرد از طریق فرآیند فشرده سازی و افزایش همزمان دمای بخار مبرد است. با این تغییر فشار، مبرد فوق گرم از طریق سیستم جریان می یابد.
کندانسور: مبدل حرارتی است که در آن مبرد تا فشار مناسب فشرده می شود و با دفع حرارت به یک محیط خنک کننده متراکم می شود.
انباشته کننده: مخزن ذخیره سازی مبرد مایع. همچنین به عنوان سرج درام شناخته می شود. معمولاً یک انباشته بر روی خط مکش قبل از ورودی پمپ در سیستم های تبرید نصب می شود تا مبرد مایع را قبل از H.P ذخیره کند. فلش درام.
H.P. فلاش درام: فلاش درام قسمت کوچکی را با فشار متوسط به مبرد می زند تا مایع مبرد باقیمانده را به حالت اشباع خنک کند، تا اثر تبرید بیشتری ایجاد کند، اساساً برای کمپرسور دو مرحله ای، فلاش درام تک مرحله ای است. استفاده شده.
شیر انبساط: دریچه ای برای کنترل جریان مبرد به اواپراتور یا چیلر.
چیلر، اواپراتور: مبدل حرارتی که در آن مبرد مایع توسط جریان فرآیندی تبخیر می شود که به نوبه خود خنک می شود.
گیرنده مبرد مایع: ظرفی در سیستم تبرید که برای اطمینان از در دسترس بودن مبرد مایع کافی برای عملکرد صحیح سیستم و ذخیره مبرد مایع در هنگام پمپاژ سیستم طراحی شده است.
گاز فلاش: گاز حاصل از تبخیر آنی مبرد توسط یک وسیله کاهنده فشار مانند شیر کنترل.
Frost Plug: نازل بسته با قطر کوچک که از کنار یک ظرف عایق بیرون زده است که با تجمع یخبندان سطح مایع را در ظرف نشان می دهد.
بای پس گاز داغ: گاز تخلیه گرم بازیافت شده به چیلر برای حفظ یکپارچگی عملکرد سیستم در شرایط حداقل بار.
سیستم کنترل
نظارت بر سیستم تبرید به ابزار دقیق مختلفی برای اندازه گیری یا کنترل متغیرهای فرآیند به شرح زیر نیاز دارد:
کنترلهای سطح: کنترلهای سطح قفس خارجی (از نوع جابجایی) رایجترین مواردی هستند که در خدمات تبرید مورد استفاده قرار میگیرند و احتمالاً مطمئنترین و آسانترین ابزار برای نگهداری هستند.
کنترل فشار: کنترل فشار مکش بالا کمپرسور مبرد ممکن است زمانی مطلوب باشد که کمپرسورهای مبرد متعدد در سیستم وجود داشته باشد.
دمای اواپراتور: دمای اواپراتور (یا چیلر) معمولاً با کنترل فشار مبرد بر روی چیلر کنترل می شود.
کنترلهای محیطی کم: همه سیستمهای تبرید باید کنترلهای محیطی پایینی داشته باشند که دمای محیط زیر ۴۰ درجه فارنهایت باشد.
این سیستم از کنترل خودکار استفاده می کند. نظارت ممکن است محلی یا یکپارچه در سیستم کنترل متمرکز کارخانه باشد.
Overview
Benefits
Delham Engineering Company designs and builds systems to site-specific requirements by engineering every Refrigeration Package with the latest process simulation software. The detailed design of the equipment considers performance, operability, reliability and safety.
Compact packaged design
Easy operation
High Refrigeration capacity
Reduced on-site time & costs
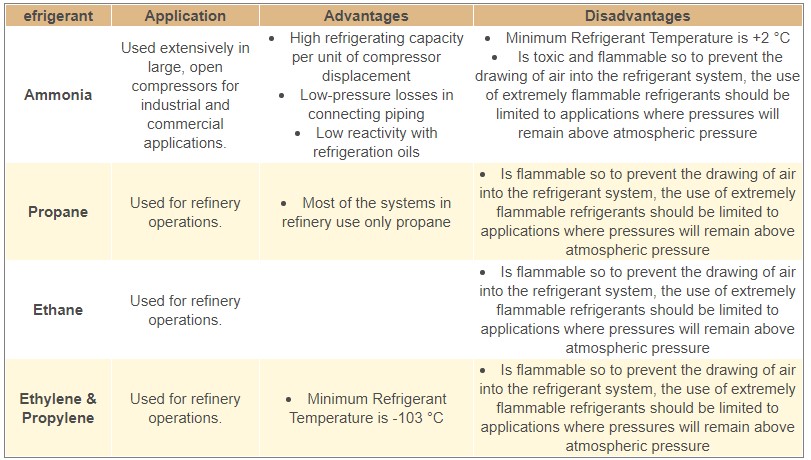
Process Description
Figure 1 shows a simplified schematic of a Refrigeration System. The compressor compresses the vaporized refrigerant and then the condenser condenses the vapor to a liquid. The liquid passes through the accumulator then expands across an expansion valve which causes it to flash and its temperature to drop substantially. The liquid portion of this flash is the refrigerant which then goes to a heat exchanger (the chiller). Basically the most common type of chiller employed in the gas processing industry is the kettle type. The refrigerant is expanded into the shell of the kettle where a level is maintained to completely submerge the process tube. In the chiller, the liquid refrigerant absorbs heat from the process stream (wet sweet gas), which lowers the process stream’s temperature to -12 °C. The heat vaporizes the liquid refrigerant. The system then returns this vapor and the vapor from the L.P. Suction Scrubber to the compressor to repeat the cycle. Vapor compression-expansion systems can be built in various sizes. These systems can also reach very low temperatures. These systems can achieve temperature -15 °C to liquefy sweet gas.
System Design
The following are the essential components of any refrigeration system:
L.P. Suction Scrubber: The gas approaching a compressor is wet. Traces of aqueous or organic liquid often intermittently and silently damage the compressor. For optimum separation performance, compressor knockout drums properly design and size with appropriate mist eliminator elements in correct configurations, taking into account many factors.
Compressor: In a refrigeration cycle, the compressor has two main functions within the refrigeration cycle. One function is to pump the refrigerant vapor from the evaporator so that the desired temperature and pressure can be maintained in the evaporator. The second function is to increase the pressure of the refrigerant vapor through the process of compression, and simultaneously increase the temperature of the refrigerant vapor. By this change in pressure the superheated refrigerant flows through the system.
Condenser: A heat exchanger in which the refrigerant, compress to a suitable pressure, is condensed by rejection of heat to a cooling medium.
Accumulator: A storage vessel for liquid refrigerant; also known as surge drum. An accumulator is usually installed on the suction line prior to the inlet of the pump in a Refrigeration Systems to store the liquid refrigerant prior to the H.P. Flash Drum.
H.P. Flash Drum: A flash drum flashes a small portion to refrigerant at the intermediate pressure to cool the remaining liquid refrigerant to the saturated condition, in order to provide a greater refrigeration effect, Basically for two-stage compressor, a single-stage flash drum is used.
Expansion valve: A valve for controlling the flow of refrigerant to an evaporator or chiller.
Chiller, Evaporator: A heat exchanger in which the liquid refrigerant is vaporized by a process stream which is in turn cooled.
Liquid refrigerant receiver: A vessel in a refrigeration system designed to ensure the availability of adequate liquid refrigerant for proper functioning of the system and to store the liquid refrigerant when the system is pumped down.
Flash gas: The gas resulting from the instantaneous evaporation of refrigerant by a pressure reducing device such as a control valve
Frost Plug: Small diameter closed nozzle protruding from the side of an insulated vessel which indicates liquid level in the vessel by accumulation of frost.
Hot gas bypass: Warm discharge gas recycled to chiller for maintaining system’s operating integrity at minimum load conditions.
Control System
The monitoring of refrigeration system requires a variety of instrumentation to measure or control the process variables as below:
Level Controls: External cage (displacer-type) level controls are the most commonly used in refrigeration services and are probably the most reliable and easy to maintain instruments.
Pressure Controls: Refrigerant compressor high suction pressure control may be desirable when there are multiple refrigerant compressors in the system.
Evaporator Temperature: The evaporator (or chiller) temperature is normally controlled by controlling the refrigerant pressure on the chiller
Low Ambient Controls: All refrigeration systems should have low ambient controls where ambient temperature is below 40°F
The system employs automatic control. Monitoring may either be local or integrated in the centralized control system of the plant.