بررسی اجمالی
جذب یک پدیده فیزیکی است که زمانی رخ می دهد که مولکول های گاز با یک سطح جامد تماس پیدا می کنند و برخی از آنها روی سطح می چسبند. آبگیری یک گاز (یا هیدروکربن مایع) با یک ماده خشک کن خشک یک فرآیند جذب است که در آن مولکول های آب ترجیحاً توسط ماده خشک کن نگه داشته شده و از جریان هیدروکربنی خارج می شوند. در طول چرخه خشک کردن، برخی از مولکولهایی که جاذب را عبور میدهند، روی سطح آن میچسبند (جذب فیزیکی بر خلاف جذب شیمیایی). پس از مدتی محدود، مولکول ها سطح جاذب را اشباع می کنند. پس از زمان کافی، حالت تعادل حاصل می شود. تعداد مولکول هایی که از سطح خارج می شوند برابر با تعداد مولکول هایی است که وارد می شوند.
تعداد مولکول هایی که روی سطح جذب می شوند تابعی از عوامل زیر است:
• ماهیت جاذب
• ماهیت مولکول جذب شده (جاذب)
• دمای سیستم
• غلظت ماده جاذب روی سطح جاذب (فاز بخار یا فاز مایع)
اگرچه چندین نظریه و مجموعه معادلات بخشی از پدیده جذب را توصیف می کنند. جذب توسط دماهای پایین و فشارهای بالا تشویق می شود و دفع توسط دماهای بالا و فشارهای پایین تشویق می شود.
فواید
شرکت مهندسی دلهام با مهندسی هر بسته جذب سطحی با جدیدترین نرم افزار شبیه سازی فرآیند، سیستم هایی را مطابق با نیازهای خاص سایت طراحی و می سازد. طراحی دقیق تجهیزات عملکرد، عملکرد، قابلیت اطمینان و ایمنی را در نظر می گیرد.
میل ترکیبی بالا برای آب
طراحی بسته بندی فشرده
عملیات آسان
ظرفیت کم آبی بالا
کاهش زمان و هزینه در محل
شرح فرایند
فرآیند جذب یک روش دستهای با بسترهای خشککننده متعدد است که در عملیات چرخهای برای خشک کردن گاز/مایع به صورت مداوم استفاده میشود.
عملکردهای جداگانه زیر باید در هر برج جاذب متناوب باشد:
• چرخه جذب یا خشک کردن گاز
• تخلیه (فقط برای آبگیرهای مایع)
• چرخه گرمایش یا بازسازی
• یک چرخه خنک کننده برای آماده سازی بستر بازسازی شده برای یک چرخه جذب دیگر
• پر کردن (فقط برای آبگیرهای مایع)
فرآیند جذب
همانطور که سیال فرآیند ورودی مرطوب (گاز یا مایع) در چرخه جذب از طریق برج به سمت پایین (برای مایع به سمت بالا) جریان می یابد، هر یک از اجزای قابل جذب با سرعت متفاوتی جذب می شوند. آب بلافاصله در لایه های بالایی بستر خشک کن جذب می شود. هر یک از هیدروکربنهای سبک و هیدروکربنهای سنگینتر که در بستر به سمت پایین حرکت میکنند نیز به میزان کم یا زیاد جذب میشوند. همانطور که لایه های بالایی ماده خشک کننده با آب اشباع می شود، آب در جریان گاز مرطوب شروع به جابجایی هیدروکربن های جذب شده قبلی در لایه های پایینی می کند. برای هر جزء در سیال فرآیند ورودی، بخشی از عمق بستر، از بالا به پایین (از پایین به بالا برای فاز مایع) وجود خواهد داشت، جایی که ماده خشککننده با آن جزء اشباع شده است و جاذب خشککننده زیر تازه شروع به جذب آن میکند. . عمق بستر از اشباع تا جذب اولیه منطقه انتقال جرم (MTZ) است که قبلا توضیح داده شد.
همانطور که جریان سیال فرآیند ادامه دارد، MTZ از طریق بستر به سمت پایین حرکت می کند و آب تمام سیال فرآیند جذب شده قبلی را جابجا می کند تا در نهایت، کل بستر با آب اشباع شود. هنگامی که بستر کاملاً از آب اشباع شود، سیال فرآیند خروجی به اندازه سیال فرآیند ورودی مرطوب است.
فرآیند بازسازی
قبل از اینکه بستر خشک کن کاملاً اشباع شود، برج ها باید از چرخه جذب به چرخه بازسازی تبدیل شوند. یک طرح بازسازی-تامین گاز شامل جریان عبوری از سیستم بازسازی است. در اکثر کارخانه ها، یک کنترل کننده جریان، حجم گاز احیا را تنظیم می کند. این گاز تا زمانی که به دمای 400 تا 600 درجه فارنهایت برسد گرم می شود، سپس به برج در حال بازسازی با لوله منتقل می شود. در صورت استفاده از گاز بازسازی خشک، آب جذب شده در شروع چرخه بازسازی شروع به جذب می کند. بخش عمده ای از آب از جاذب ها در دمای 240 درجه فارنهایت تا 250 درجه فارنهایت حذف می شود، اما دفع ادامه می یابد، اگرچه با سرعتی پیوسته کاهش می یابد، تا پایان چرخه گرمایش. پس از حذف تمام آب، گرمایش برای دفع هر گونه هیدروکربن سنگین و آلاینده ای که در دماهای پایین تر تبخیر نمی شود حفظ می شود. هنگامی که دمای گاز خروجی (اوج خروجی) به 350 درجه تا 550 درجه فارنهایت رسیده باشد، بستر خشک کننده به درستی بازسازی می شود. پس از چرخه گرمایش، بستر خشککننده با جریان گاز احیا نشده خنک میشود تا زمانی که ماده خشککننده به اندازه کافی خنک شود. تمام گاز احیا که در چرخه های گرمایش و سرمایش استفاده می شود از یک مبدل حرارتی عبور می کند و در آنجا خنک می شود تا آب خارج شده از بستر خشک کننده بازسازی شده متراکم شود. این آب در جداکننده گاز احیا جدا می شود و گاز با جریان گاز مرطوب ورودی مخلوط می شود. کل این فرآیند پیوسته و خودکار است. برج های جاذب باید از سرویس خشک کردن خارج شوند تا بازسازی شوند. به همین دلیل، خشک کن های جامد معمولاً از دو، سه یا چهار برج جاذب استفاده می کنند. برخی از برنامه ها از دوازده برج استفاده می کنند. در برخی شرایط برای سه یا چند طرح برج جاذب مزایای اقتصادی و فرآیندی وجود دارد.
آبگیری دو برج
دستگاه های خشک کن جامد با استفاده از دو برج جاذب تنها یک آرایش جریان را ارائه می دهند. در حالی که یک برج جریان سیال فرآیند را کم آب می کند، برج دیگر بازسازی می شود. دو برج به طور متناوب بین خشک شدن و بازسازی می شوند.
آبگیری سه برج
آبگیرهای خشک کن جامد با سه برج جاذب، تغییرات زیادی در جریان فرآیند ارائه می دهند. چرخه فرآیند سه برج ممکن است طوری تنظیم شود که دو برج به طور موازی آبگیری کنند در حالی که یک برج بازسازی می شود. یا، چرخه فرآیند ممکن است طوری تنظیم شود که یک برج در حال جذب، یک برج در حال بازسازی و یک برج در حال خنک شدن باشد.
آبگیرهای چهار برجی
آبگیرهای خشک کن جامد که از چهار برج جاذب استفاده می کنند، تغییرات زیادی در جریان فرآیند ارائه می دهند. روش دیگر، آبگیرها ممکن است سه برج در حال خشک شدن داشته باشند در حالی که یک برج بازسازی و خنک می شود.
طراحی سیستم
موارد زیر اجزای ضروری هر سیستم آبگیری خشک کن جامد هستند:
جداکننده جریان گاز ورودی / کوالسر مایع.
دو یا چند برج جذب (کنتاکتور) پر شده با ماده خشک کن جامد.
یک بخاری با دمای بالا که گاز احیاگر داغ را برای فعال کردن مجدد ماده خشک کن در برج ها فراهم می کند.
یک کولر گازی احیا کننده که آب را از گاز داغ احیا می کند.
جداکننده گاز احیا (ناک اوت) که آب متراکم شده را از گاز احیا حذف می کند.
منیفولدهای لوله کشی، شیرهای سوئیچینگ و کنترل هایی که جریان گازها را بر اساس نیاز فرآیند هدایت و کنترل می کنند.
Overview
Adsorption is a physical phenomenon that occurs when molecules of gas are brought into contact with a solid surface and some of them adhere on the surface. Dehydration of a gas (or liquid hydrocarbon) with a dry desiccant is an adsorption process in which water molecules are preferentially held by the desiccant and removed from the hydrocarbon stream. During the drying cycle some molecules passing the adsorbent adhere on its surface (physical adsorption as opposed to chemical absorption). After some finite time the molecules saturate the surface of adsorbent. After sufficient time, a state of equilibrium is reached; the number of molecules leaving the surface equals the number arriving.The number of molecules adsorbing on the surface is a function of the following factors.
The nature of the adsorbent
The nature of the molecule being adsorbed (the adsorbate)
The temperature of the system
The concentration of the adsorbate over the adsorbent surface (vapor-phase or liquid-phase)
Although several theories and sets of equations describe a part of the adsorption phenomenon. Adsorption is encouraged by low temperatures and high pressures, and desorption is encouraged by high temperatures and low-pressures.
Benefits
Delham Engineering Company designs and builds systems to site-specific requirements by engineering every Adsorption Package with the latest process simulation software. The detailed design of the equipment considers performance, operability, reliability and safetyHigh affinity for water.
Compact packaged design
Easy operation
High dehydration capacity
Reduced on-site time & costs
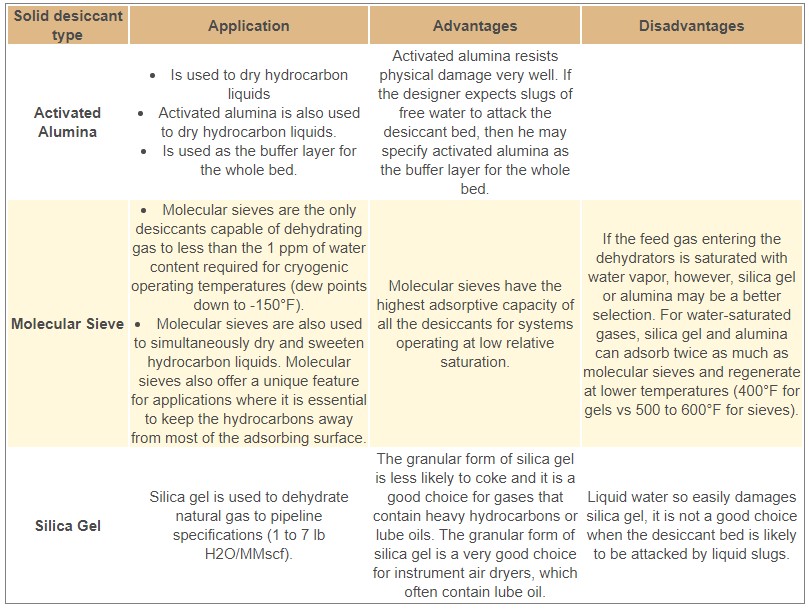
Process Description
The adsorption process is a batch procedure with multiple desiccant beds used in cyclic operation to dry the gas/liquid on a continuous basis
The following separate functions must alternate in each adsorber tower.
An adsorbing or gas-drying cycle
Draining (for liquid dehydrators only)
A heating or regenerating cycle
A cooling cycle to prepare the regenerated bed for another adsorbing cycle
Filling (for liquid dehydrators only)
Process of Adsorption
As the wet inlet process fluid (gas or liquid) flows downward(upward for liquid) through the tower on the adsorption cycle, each of the adsorbable components is adsorbed at a different rate. The water is immediately adsorbed in the top layers of the desiccant bed. Each of the light hydrocarbon and heavier hydrocarbons moving down through the bed are also adsorbed to a greater or lesser extent. As the upper layers of desiccant become saturated with water, water in the wet gas stream begins displacing the previously adsorbed hydrocarbons in the lower layers. For each component in the inlet process fluid, there will be a section of bed depth, from top to bottom (bottom to top for liquid phase), where the desiccant is saturated with that component and where the desiccant below is just starting to adsorb it. The depth of bed from saturation to initial adsorption is the mass transfer zone (MTZ) described earlier.
As the flow of process fluid continues, the MTZ’s move downward through the bed and water displaces all of the previously adsorbed process fluid until, finally, the entire bed is saturated with water. When the bed is completely saturated with water, the outlet process fluid is just as wet as the inlet process fluid.
Process of Regeneration
Before the desiccant bed has become completely saturated, the towers must be switched from the adsorption cycle to the regeneration cycle. One regeneration-gas-supply scheme consists of the stream through the regeneration system. In most plants, a flow controller regulates the volume of regeneration gas used. This gas is heated until it reaches 400° to 600°F, then it is piped to the tower being regenerated. The adsorbed water begins to desorb at the start of the regeneration cycle if dry regeneration gas is used. The bulk of the water is removed from the adsorbents at a temperature of 240°F to 250°F, but the desorption continues, although at a continually diminishing rate, until the end of the heating cycle.After all the water has been removed, heating is maintained to drive off any heavier hydrocarbons and contaminants that do not vaporize at lower temperatures. The desiccant bed is properly regenerated when the outlet gas (peak-out) temperature has reached 350° to 550°F. After the heating cycle, the desiccant bed is cooled by flowing unheated regeneration gas until the desiccant is sufficiently cooled. All of the regeneration gas used in the heating and cooling cycles is passed through a heat exchanger where it is cooled to condense the water removed from the regenerated desiccant bed. This water is separated in the regeneration gas separator, and the gas is mixed with the incoming wet-gas stream. This entire process is continuous and automatic.Adsorber towers must be taken out of drying service to be regenerated. Because of this, solid desiccant dehydrators typically use two, three, or four adsorber towers. Some applications use as many as twelve towers. There are economic and process advantages for three or more adsorber tower designs in some situations.
Two-Tower Dehydrators
Solid desiccant dehydrators using two adsorber towers offer only one flow arrangement. While one tower dehydrates the process fluid stream, the other tower regenerates. The two towers alternate between drying and regeneration.
Three-Tower Dehydrators
Solid desiccant dehydrators with three adsorbing towers offer several process flow variations. The process cycle of three towers may be arranged so that two towers dehydrate in parallel while one tower regenerates. Or, the process cycle may be arranged so that one tower is adsorbing, one tower is regenerating, and one tower is cooling.
Four-Tower Dehydrators
Solid desiccant dehydrators that use four adsorber towers offer several process flow variations. Alternatively, dehydrators may have three towers drying while one tower regenerates and cools.
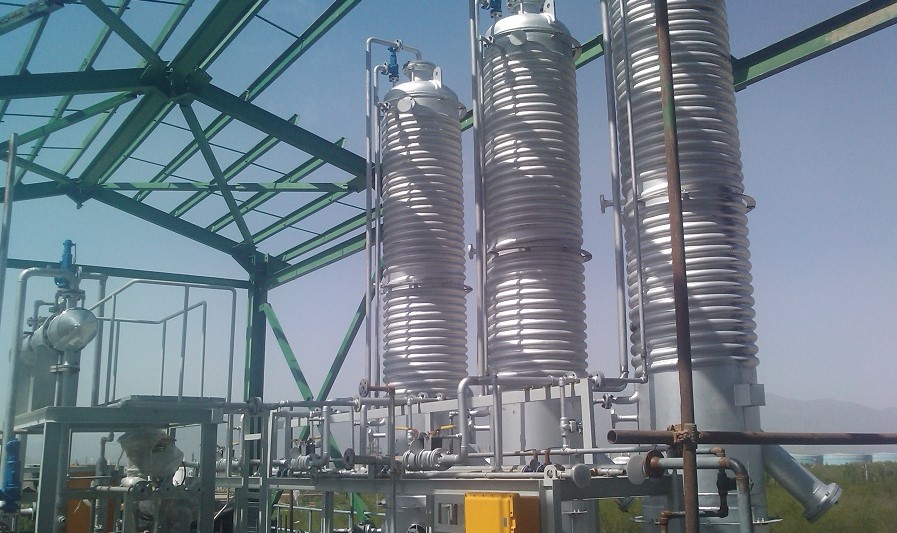
System Design
The following are the essential components of any solid desiccant dehydration system An inlet gas stream separator/liquid coalescer.
Two or more adsorption towers (contactors) filled with solid desiccant.
A high-temperature heater that provides hot regeneration gas to reactivate the desiccant in the towers.
A regeneration gas cooler that condenses water from the hot regeneration gas.
A regeneration gas separator (knockout) that removes the condensed water from the regeneration gas.
Piping manifolds, switching valves, and controls that direct and control the flow of gases according to the process requirements.
Control System
The monitoring of solid desiccant dehydrators requires a variety of instrumentation to measure or control the following process variablesFlow rate, temperature, and pressure of the process fluid.
Water content of the product fluid
Flow rate and pressure of the regeneration gas
Inlet and outlet temperatures of the regeneration gas
Temperature of the regeneration gas leaving the regeneration gas cooler
Adsorbent differential bed pressure
Cycle time controllers
The system employs automatic control. Monitoring may either be local or integrated in the centralized control system of the plant.